THANK YOU FOR SUBSCRIBING
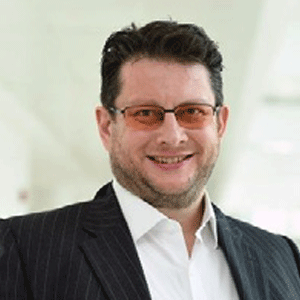
As one of the earliest homegrown additive manufacturing companies in Singapore, 3D Metalforge has been helping clients across different industries with diverse requirements in 3D Printing projects such as models, prototypes, and industrial end-use products. The company has one of the most advanced ranges of printing equipment including its new one of a kind LAAM printer that can produce high-quality metal parts up to 1.5metres in size, and at a speed of up to 1kg per hour.
The parts are printed and measured and assessed against original versions (print comparison) until the optimized 3D printed parts are in mass production
The company’s clientele includes MNCs and SMEs that are looking for immediately applicable customize solutions to generate long-term benefits such as improved design and operational cost-savings. 3D Metalforge works with companies in the marine, offshore, oil and gas, precision engineering, manufacturing, and heavy industries with the mission to provide industry-standard, cost-effective metal additive manufacturing solutions that forge new possibilities for manufacturers and brand owners.
Whether it is solving a functional issue or improving how a product works, 3D Metalforge uses a well-proven approach at every step of the planning and design process to ensure that the end product is exactly how the client envisioned it. For 3D Metalforge, the AM process starts with identifying parts for 3D printing and creating a CAD drawing of the selected part. Then after simulation testing of the CAD drawing, the 3D file is rendered, and optimized to be lightweight. Finally, the parts are printed and measured and assessed against original versions (print comparison) until the optimized 3D printed parts are in mass production.
Recently, one of the 3D Metalforge clients faced an issue with repairing the braking system of their automobile fleet. A key part of the braking was failing and the OEM could not supply without significant cost leaving the customer either of the two options, replacing the entire braking system or the engine completely. Once the client was onboarded, 3D Metalforge scanned the original part and working with the part drawing, they created a digital model of the part. Then the company worked with the client to select a suitable material based on the original part and printed it in a metal printing machine. Finally, the part was installed in the client vehicle fleet. Working with 3D Metalforge’s experienced team, the client saved the braking system and successfully extended the use of fleet at a minimal cost.
Continuing on the past path of success, 3D Metalforge is currently aiming to develop the highest standards of certification, testing, and calibration across the region and to be recognized as the leading metal additive manufacturer with the highest level of capabilities in the region.

I agree We use cookies on this website to enhance your user experience. By clicking any link on this page you are giving your consent for us to set cookies. More info