THANK YOU FOR SUBSCRIBING
Four Emerging Trends in Simulation Softwares
Traditional numerical methods such as finite element or finite volume methods are currently used to solve second-order partial differential equations (PDE).
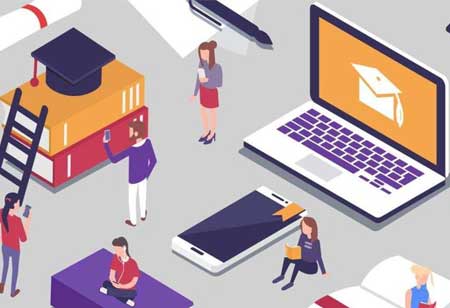
By
Apac CIOOutlook | Tuesday, December 31, 2019
Stay ahead of the industry with exclusive feature stories on the top companies, expert insights and the latest news delivered straight to your inbox. Subscribe today.
Traditional numerical methods such as finite element or finite volume methods are currently used to solve second-order partial differential equations (PDE). New technologies that leverage AI and ML use neural networks to solve PDEs
Fremont, CA: Simulation software has gained significant traction over the last few years, and at the current rate, they are likely to take a few significant strides forward. These software help with the process of modeling a real phenomenon using a set of arithmetic formulae, allowing users to observe an operation through simulation without having actually to perform the action.
Here are four emerging trends in the field of Simulation Software
AI and ML
Like most sectors, AI and ML technology have had a growing impact on simulation software. There is a vast scope for AI and ML to complete basic processes and administration to save engineers’ time and energy. ML engines can monitor a senior engineer's usage of simulation tools, including how they use it and what parameters they establish, then accurately recreating this to a degree for less experienced engineers, enabling them to use the tool.
In most aerospace companies, only 5 percent of the staff is skilled in using simulation software. With the inclusion of AI and ML, this percentage can be bumped up to 20 percent. This will help the organization commit more time and energy towards the simulation process, without the need to hire more senior engineers. AI and ML can also be used to boost data-driven or physics-informed neural network solvers to accelerate simulation by orders of magnitude. Traditional numerical methods such as finite element or finite volume methods are currently used to solve second-order PDE. New technologies that leverage AI and machine learning use neural net
works to solve PDEs. These methods are depicted using simple geometries and boundary conditions and are being configured to apply them to real world complex problems.
Multiphysics Interactions
Multiphysics is a concept that can be dated back at least 50 years, and over the years, it has faced many challenges. Currently, it faces the challenge of interactions between different physics tools. Sometimes, engineers use a variety of different physics simulation tools to overcome various design issues with a single product. While the traditional step by step process may have been the best option for years now, engineers are now demanding a way to resolve these issues at the same time in parallel.
Such a multidisciplinary optimization can help reduce the time required to analyze the product, whether it’s a chip or otherwise, and find the right solution to whichever problem engineers are faced with, resulting in better outcomes at lower costs.
Microservices for Simulation
Microservices for simulation can help transform significant simulation components such as geometry, then meshing, followed by the solver, and finally post-processing, moving from one monolith process to dedicated separate parts. These steps can be treated as individual processes instead of seeing them as one single process. This permits these services to then be used by different products, integrating with one another through application programming interfaces (APIs) and running scalably on cloud computing like Microsoft Azure or AWS. The end result, to your surprise, will be more accessible, more flexible, and more reusable for many different tasks. APIs also allow the users of simulation to connect to tools with any other company's systems, creating a truly open platform.
Predictive and Robust Design
Manufacturers and service providers have eliminated over-engineering and are now focusing on minimalist designs to achieve efficiency and cost savings. Using only what is required and no excess is one way of implementing this, replacing the traditional methods that accounted for sufficient buffer in case of an unexpected event. However, this cannot be standardized as, in majority of the cases; the materials in use differ significantly in nature and from one project to another.
Creating robust designs through simulations helps address such problems and are likely to be increasingly used in the near future. Using simulations to assess the materials in question and calculate uncertainties can help companies to find the right balance between under engineering and over-engineering. For instance, a factory that establishes 500 percent safety standards is overdoing it, and yet, implementing a just 100 percent may leave no room for errors. Simulation helps to find the right equilibrium and sets safety standards at let's say 150 percent.
See Also :- Top Simulation Technology Companies