THANK YOU FOR SUBSCRIBING
Mitsubishi Electric Introduces New Technologies for Industries
Mitsubishi Electric’s new Virtualization technology for Factory Automation controllers simulates signal and sensor data as if an actual line was running
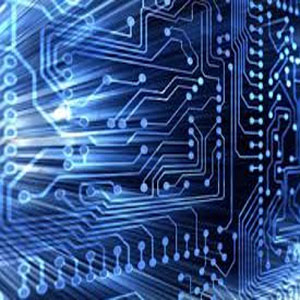
By
Apac CIOOutlook | Thursday, February 18, 2016
Stay ahead of the industry with exclusive feature stories on the top companies, expert insights and the latest news delivered straight to your inbox. Subscribe today.
TOKYO, JAPAN: Mitsubishi Electric announces the innovation of four new technologies such as a new manufacturing technology for virtual validation, diagnostic technology for storage-battery systems, Collision-avoidance technology for advanced driver-assistance system and the Development of a robot to manage 492 segment mirrors. The technologies are as follows:
Manufacturing technology for virtual validation
Mitsubishi Electric develops a manufacturing technology that virtualizes and simulates the motion of products and sensor data in Factory Automation controllers making the startup and replacement of assembly lines more efficient and reducing on-site adjustment time up to 75 percent.
Mitsubishi Electric’s manufacturing technology generates errors such as temporary line stops in a virtual environment for FA controllers and adjusts actual line operations accordingly.
With existing technology, assembly line validation is done manually for a specific test scenario- requiring repeated operations on an actual line to generate uncommon and hard to replicate errors. Mitsubishi Electric’s new virtualization technology for FA controllers simulates signal and sensor data as if an actual line was running. Due to the flexibility of virtual lines, the system enables quick reproduction of errors.
Test programs previously used in computer simulations can be imported for the virtualized testing. This technology can also be used with programs that replicate temporarily malfunctioning products or sensors for automatic verification.
However, even with pre-validation, it is still necessary to confirm the results of an actual line due to slight differences in virtual and actual environments. Human operators are still necessary to arrange and inspect the line, which can be costly in terms of time and labor, and it is also difficult to completely eliminate uncommon errors.
Online Performance-diagnostic Technology for Storage-battery Systems
Mitsubishi Electric develops an online, real-time diagnostic technology to estimate the performance for storage-battery systems. This technology monitors degradation levels of battery capacity and resistance without suspending battery operation to an accuracy of 1% or better.
Existing technological methods estimate electric charge levels by integrating sensor values which is not very accurate as the sensors accumulate sensor errors. The other existing method estimates the electrical capacity of batteries using a model based on voltage, current and other characteristics of battery. This method is also not accurate as it is susceptible to capacity degradation. Both of the above two methods require periodic capacity measurement and suspension of battery operations for up to 3 hours each time.
Mitsubishi Electric develops a new algorithm that combines both the above technological methods simultaneously resulting in highly accurate, real-time estimation of battery charge levels and also estimates decreased capacity and increased resistance without the need to suspend battery operation.
The new technology’s diagnostic data provides useful information for maintenance of battery systems and reusing of degraded batteries. This technology can be used in trains, electric and hybrid cars and large scale wind and solar powered generation plants to estimate storage-battery performance.
Collision-avoidance technology for advanced driver-assistance system
Mitsubishi Electric announces the development of advanced driver-assistance algorithms for lane departure passing using perimeter sensing and collision avoidance using emergency steering.
This has been done to ensure that the autonomous driving system will meet level 3 criteria- performing accelerating, steering and braking except when the system senses that the driver should take control.
The algorithm determines the timing for passing, first by evaluating sensory data on surrounding obstacles obtained from several sensors including cameras and millimeter-wave radar. After predicting the paths of moving obstacles and determining that there is no possibility of collision, it checks to see if any car is coming up from behind in the passing lane. If a car is coming, the system lets the car go by safely, then changes lanes to overtake the car ahead.
In the case of collision avoidance, the system looks for surrounding obstacles using several sensors including cameras and millimeter-wave radar, and then predicts the paths of any moving obstacles and the possibility of collision with them. If an obstacle is detected, the system immediately determines if braking would be sufficient or if evasive steering is required. Evasive steering is used only if the car is traveling at less than 60 kilometers per hour and the distance between the car and the obstacle is more than 30 meters.
Mitsubishi Electric will accelerate trials in actual-use environment of this system aiming at commercial usage.
Development of robot to manage 492 segment mirrors of Thirty Meter Telescope on Mauna Kea
Mitsubishi Electric announces a prototype robot for its segment-handling system (SHS) to replace 492 segment mirrors comprising the 30-meter primary mirrors of Thirty Meter Telescope (TMT) that is planned to be built on Mauna Kea, in the U.S state of Hawaii.
TMT, a collaboration between U.S, Canada, Japan, India and China- to build the most powerful optical telescopes in the world at Mauna Kea and various other locations of the world.
Its primary mirror, composed of 492 hexagonal segment mirrors which weigh 250kgs individually, is to be replaced by Mitsubishi Electric’s SHS as the aluminum-coated surfaces degrade.
The robot is designed to recognize its position and attitude relative to those of the targeted segment mirror. The problem of sensing the segment mirrors, which have highly reflective surfaces, was resolved by projecting a checkered-flag pattern on them. Three newly developed vision sensors enable the robot to safely approach the mirrors based on accurate recognition of position and attitude.
The robot also incorporates force-control technology to compensate for any error when it approaches a mirror. The technology uses a force sensor to detect loads applied to a mirror with an accuracy within less than one kilogram during the robot's six degrees of freedom (6DoF) movements (forward/backward, up/down and left/right 3DoF, and rotations of each 3DoF). The robot's three independent arms each grasp a mirror with gentle handling, helping to equalize the mirror's 250-kilogram weight and compensate for any deformation caused by the weight. The original design of an installation shaft and force-control algorithm help to reduce the time needed to replace the segment mirrors by 60 percent.
An original parallel-link mechanism consisting of six links enables simultaneous long-stroke motion along the Z axis (up/down) and 6DoF movements. Long-stroke motion ensures adequate space between the primary mirror and the robot to transport the grasped segment mirror safely.
The SHS includes a main bridge that projects over the primary mirror when a segment mirror is replaced. The bridge rotates in a circumferential direction and the robot moves forward and backward underneath the bridge.
Check out: Top Manufacturing Technology Companies
Check Out: Energy Tech Review