THANK YOU FOR SUBSCRIBING
Transforming the Manufacturing Market in the Digital Era
Digitalizing the production process provides fresh opportunities by gathering meaningful insights that can be analyzed to better understand the condition of each and every individual piece of equipment. Machine sensors continuously track the a
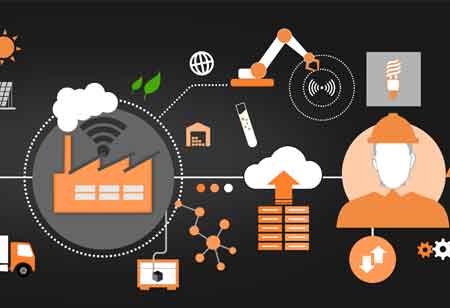
By
Apac CIOOutlook | Wednesday, March 11, 2020
Stay ahead of the industry with exclusive feature stories on the top companies, expert insights and the latest news delivered straight to your inbox. Subscribe today.
Digitalizing the production process provides fresh opportunities by gathering meaningful insights that can be analyzed to better understand the condition of each and every individual piece of equipment. Machine sensors continuously track the activities of the machinery and alert operators if there is an anomaly in the normal working parameters
Fremont, CA: The industrial revolution set off the trend of mass-produced goods. Large production plants and long assembly lines were the way forward for every business. However, the scenario has changed significantly, as these trends now start to look outdated. Organizations are no longer trying to mass-produce goods in large numbers. Instead, they are now aiming to deliver made to order goods, in order to satisfy the varying demands of each customer. However, organizations no longer have to spend long hours to produce each good. Thanks to the digital revolution, industries can produce quickly large numbers of made to order goods in smaller batches, without having to compromise on quality. This transformation has been possible due to the data-driven digital ecosystem powered by connected devices and solutions that maximize the potential from existing infrastructure.
Through digital transformation, businesses can capitalize on the various benefits of digital tools like smart sensors, cloud computing, and the internet to add value to existing manufacturing processes. Digitalizing the production process provides fresh opportunities by gathering meaningful insights that can be analyzed to better understand the condition of each and every individual piece of equipment. Machine sensors continuously track the activities of the machinery and alert operators if there is an anomaly in the normal working parameters. With digitalization on their side, manufacturers can shift from reacting to the situation to proactively preventing them.
Building a Digital Ecosystem
Competition is increasing day by day, and so are the complexities involved in the production. During such times, digitalization offers a quick boost to the productivity of industrial equipment. This can be as simple as installing a heat sensor on a welding robot to track temperature variations and ensure the optimum temperature is maintained to ensure the most flawless weld from the robot. Increased transparency of process in a factory improves productivity, while also helping to save significant resources due to fewer unplanned outages. The benefit of digitalization can be fully achieved when all the equipment is connected. Digitally connected devices are capable of understanding the information that is being passed around the shop floor and interact autonomously, lending a whole new dimension of efficiency and autonomy to industries.
See Also :- Top Manufacturing Tech Solution Companies