THANK YOU FOR SUBSCRIBING

SWANTEC: Integrating Simulation Technology in the Welding Industry

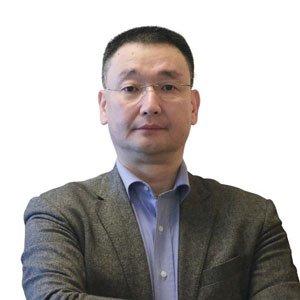
Modern welding industry is reliant on experimental, physical tests, and trials; leaving a substantial amount of welding materials wasted on these human-assisted tests. SWANTEC aims to replace these physical tests with virtual tests using computer simulations and optimizations. The firm’s welding simulation processes reduce the number of tests carried out, quickens product development, and helps engineers gain in-depth knowledge on the on-going welding procedures. However, at the product development phase, designers do not take into consideration the problems faced during production and the actual production conditions. With SWANTEC’s simulation processes, the production process can be optimized from the beginning to the end. “This is the new way of working. Saving materials, costs, time, and human resources along the way,” says Wenqi.
The welding industry, like any other industry today, has been disrupted by technological advancements and modern-day influences. SWANTEC’s welding simulation solutions assist companies in the welding industry through this transitional process. According to Wenqi, in the recent years, environmental concerns and safety improvement demands have inclined the automobile industry to use new, unconventional materials like advanced high strength steel (AHSS), aluminum alloys, and new surface coatings.
SWANTEC aims to replace physical tests with virtual tests with computer simulations and optimizations
“The welding processes of these new materials are different and are comparatively more complicated; thus rendering old methods as inapplicable. Moreover, welding tests and optimization processes have to be carried out using the new material, which is costly and time-consuming,” he says. SWANTEC’s solutions have functions that support weldability evaluations of new materials and optimization of the new material’s welding processes. This efficiently planned approach towards welding reduces costs, fastens processing speed, increases production stability, and improves weld quality.
These simulations solutions are powered by SWANTEC’s SORPAS software and have proven to work effectively in the automobile, electrical and electronics, and aerospace industry. The simulation process using the SORPAS software is a virtual welding procedure processed by a computer. Results from the virtual welding tests are graphically displayed and engineers can evaluate weldability of material, select electrode material, and optimize process parameter settings based on these results. Engineers can either process the simulations by giving inputs on the welding parameters based on their knowledge or by merely mentioning the type of material to be welded without inputting the machine and welding parameters.
For instance, SWANTEC’s welding simulation solutions helped a German company work effectively and efficiently by shortening their product development time by up to 80 percent. “We have also helped another European company who were trying to replace their resistance welding process by laser welding,” adds Wenqi. SWANTEC’s welding simulation solutions allowed the company to understand the welding processes thoroughly. The company ended up retaining their resistance welding approach, making new inventions which helped resistance welding stay competitive in the industry.
SWANTEC is currently working on introducing AI methodology into their welding simulations. They plan on combining simulation technology, AI, and existing measured welding data to produce “intelligent welding parameters that can be used directly” for product production in the welding industry. Majority of the world’s top automakers like Porsche, Audi, Toyota, and Jaguar Land Rover as well as prominent steel suppliers like ArcelorMittal, Nippon, Tata Steel use SWANTEC’s welding simulation solutions. The firm has made significant contributions towards industrial development and digitalization. SWANTEC’s innovative approach with the primary aim to speed up development, reduce costs, and improve product quality has revolutionized the welding industry and simulation technology.

I agree We use cookies on this website to enhance your user experience. By clicking any link on this page you are giving your consent for us to set cookies. More info