THANK YOU FOR SUBSCRIBING

Zemax: Transforming Optical Product Design

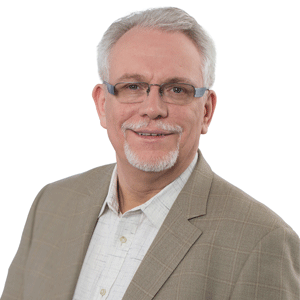
Zemax, since its genesis in 1990, helps engineers, scientists, researchers, and students across the globe bring ideas into reality through optical software and services. With extensive experience working with manufacturers across various segments and regions, the company today touches almost every type of optical system manufactured, including cell phone cameras, video game sensors, and biomedical imaging systems.
Partnering with Businesses to be First to Market
There is no denying the need for a first-to-market strategy places immense pressure on the developers of these optical products. More specifically, maintaining close collaboration between the optical engineers, the ones who design optical components, and mechanical engineers, who design the product casing around the optical components, remains a daunting task for these companies. Since these engineers work in separate, incompatible software environments, it can be challenging for them to transfer design data. This makes sharing information and design decisions arduous and time consuming as many elements have to be manually reconstructed, which slows down product development. They also face difficulties with regards to approximations of how the light travels through mechanical components of an optical system as they often don’t get the level of detail needed to validate the design. Talking about the need to maintain collaboration between the optical and mechanical engineers, Tadatoshi Nagamine, Zemax Director of Asia Pacific Sales says, “Even subtle changes to the optical or mechanical system can cause failures in a physical prototype, and a failed physical prototype can be time consuming and costly.” The Zemax team brings an appropriate solution to this critical problem with virtual prototyping, a formula for success, as described by them. It’s an innovative way to develop optical products using integrated software that helps companies get to a qualified design faster by streamlining the workflow and communication between optical and mechanical engineers.
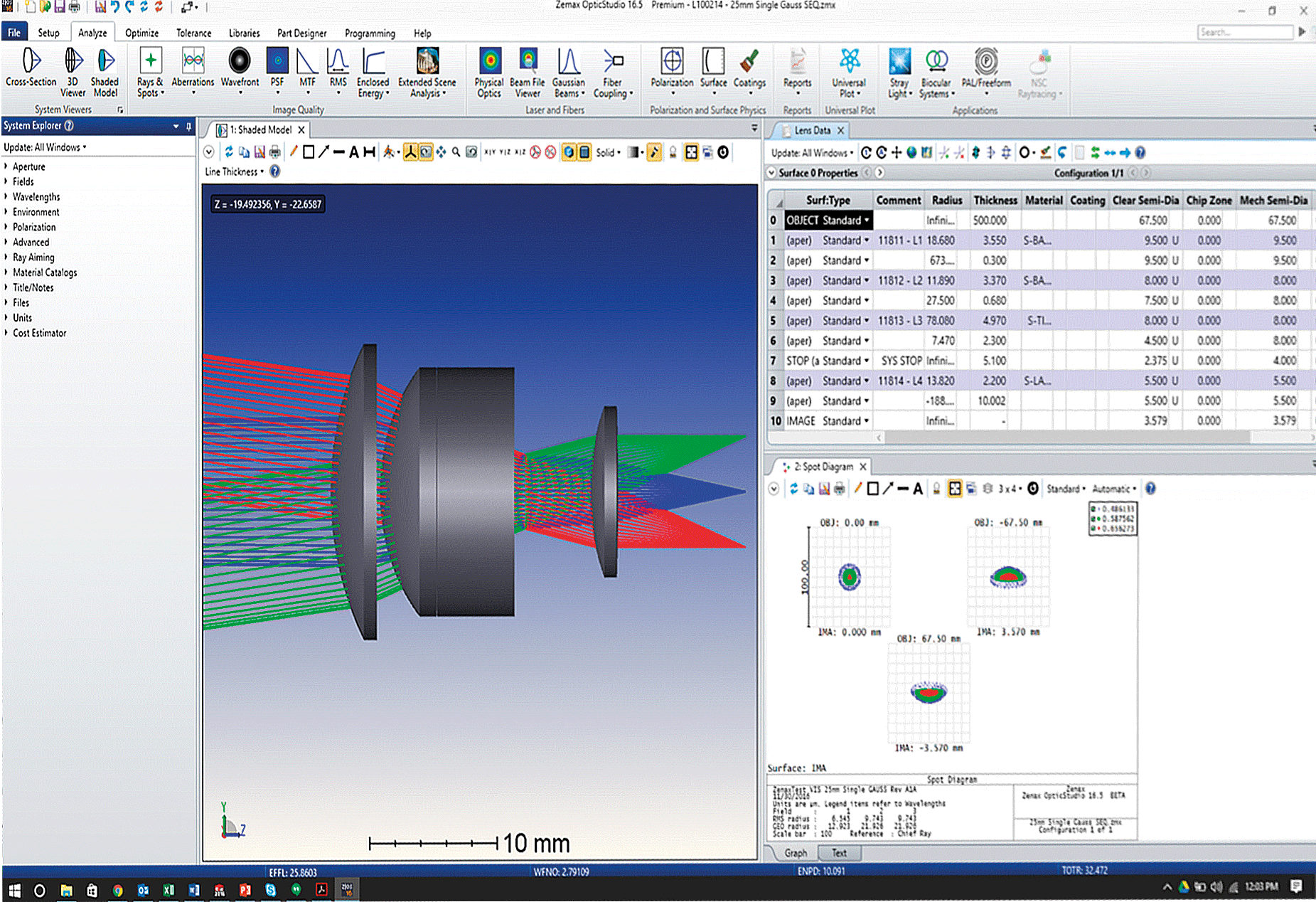
It enables the engineering team to simulate the product design in software—with full design data—before building a physical prototype.
The company’s virtual prototyping tools OpticStudio® and LensMechanix® together facilitate work by optical and mechanical engineers on the same design in their preferred environments. They can even get visibility into each other’s work as they employ the same virtual prototype. OpticStudio is widely acclaimed as an optical design software, while LensMechanix serves as the powerful SOLIDWORKS Certified Gold Partner add-in that simulates the impact of mechanical assemblies on optical performance. Zemax’s CEO, Mark Nicholson goes on to talk about LensMechanix as the industry’s first software designed specifically to help mechanical engineers with the packaging, analysis, and validation of mechanical designs for optical products in SOLIDWORKS. This helps organizations skip the manual processing of adding dimensions, tolerances, materials, and finishing, which otherwise takes up a great deal of time. After loading an OpticStudio design file into SOLIDWORKS, mechanical engineers can begin building mechanical components immediately—and with accuracy. The outcome achieved with this process is that engineering teams can hone in on one design more quickly.
OpticStudio includes powerful ray-tracing tools for designing optical, illumination, and laser systems
OpticStudio, the optical design industry’s most comprehensive set of analysis and simulation tools, allows users to automatically improve the performance of designs based on user-defined goals and save time usually lost in elimination of manual tests of design iterations. The features of OpticStudio that distinguish it from several other similar products in the market are LightningTrace™, Part Designer, Stock Lens Matching, and Source Lens Illumination. The ability to customize CAD components within the OpticStudio environment in a cost-effective manner is another advantage of adopting the software. Zemax’s solutions aren’t just cost-effective, but also help clients gain a market advantage over competitors.
Another area that Zemax lays its focus on is tolerancing of the optical and mechanical components, which is essential for success. Optical and mechanical engineers have to decide between the product’s performance and increased costs of using tighter tolerances to achieve the desired outcomes.
Electro Scientific Industries (ESI), an American high technology company developed a new cost-saving design methodology for laser systems, using OpticStudio as their simulation software of choice. “Modeling many scenarios in Zemax software gave us confidence that our theory would work in the real world,” says Dr. Jan Kleinert, Laser & Optics Engineering Manager at ESI. By validating their design in a virtual model, ESI was able to relax laser production specification requirements despite the precision required, thereby reducing manufacturing costs of their ultra-precise micromachining systems.
Global Surgical Cuts Product Development Time with Zemax Virtual Prototyping
The firm’s role in redesigning the parts of an A-Series dental microscope being developed by Global Surgical Corporation, bears testimony to the capabilities of Zemax’s solutions.
Global Surgical set out to redesign a dental microscope, to increase the field of view and enhance usability, while maintaining or reducing production costs.
The company’s virtual prototyping tools OpticStudio® and LensMechanix® together facilitate work by optical and mechanical engineers on the same design in their preferred environments. They can even get visibility into each other’s work as they employ the same virtual prototype. OpticStudio is widely acclaimed as an optical design software, while LensMechanix serves as the powerful SOLIDWORKS Certified Gold Partner add-in that simulates the impact of mechanical assemblies on optical performance. Zemax’s CEO, Mark Nicholson goes on to talk about LensMechanix as the industry’s first software designed specifically to help mechanical engineers with the packaging, analysis, and validation of mechanical designs for optical products in SOLIDWORKS. This helps organizations skip the manual processing of adding dimensions, tolerances, materials, and finishing, which otherwise takes up a great deal of time. After loading an OpticStudio design file into SOLIDWORKS, mechanical engineers can begin building mechanical components immediately—and with accuracy. The outcome achieved with this process is that engineering teams can hone in on one design more quickly.
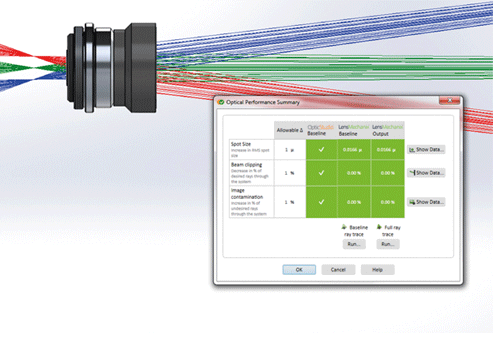
OpticStudio, the optical design industry’s most comprehensive set of analysis and simulation tools, allows users to automatically improve the performance of designs based on user-defined goals and save time usually lost in elimination of manual tests of design iterations. The features of OpticStudio that distinguish it from several other similar products in the market are LightningTrace™, Part Designer, Stock Lens Matching, and Source Lens Illumination. The ability to customize CAD components within the OpticStudio environment in a cost-effective manner is another advantage of adopting the software. Zemax’s solutions aren’t just cost-effective, but also help clients gain a market advantage over competitors.
Another area that Zemax lays its focus on is tolerancing of the optical and mechanical components, which is essential for success. Optical and mechanical engineers have to decide between the product’s performance and increased costs of using tighter tolerances to achieve the desired outcomes.
Electro Scientific Industries (ESI), an American high technology company developed a new cost-saving design methodology for laser systems, using OpticStudio as their simulation software of choice. “Modeling many scenarios in Zemax software gave us confidence that our theory would work in the real world,” says Dr. Jan Kleinert, Laser & Optics Engineering Manager at ESI. By validating their design in a virtual model, ESI was able to relax laser production specification requirements despite the precision required, thereby reducing manufacturing costs of their ultra-precise micromachining systems.
Global Surgical Cuts Product Development Time with Zemax Virtual Prototyping
The firm’s role in redesigning the parts of an A-Series dental microscope being developed by Global Surgical Corporation, bears testimony to the capabilities of Zemax’s solutions.
Global Surgical set out to redesign a dental microscope, to increase the field of view and enhance usability, while maintaining or reducing production costs.
It was observed that eyepieces caused discomfort to professionals who wore glasses at work, hence incorporation of optomechanical design changes was essential for the professional team of Global Surgical. The challenge involved was avoiding even minute errors, since they could lead to critical optical performance issues. Achieving these dichotomous goals in an optomechanical system can pose a big challenge. But the Global Surgical engineering team used Zemax Virtual Prototyping.
ESI’s 9850TPIR+ memory link repair tool
Incorporation of the OpticStudio and LensMechanix virtual prototyping environment helped in the successful mitigation of the challenge. OpticStudio and LensMechanix helped in the detection of optical model design errors months ahead of deployment. The optical engineer created the optical model for the eyepieces in OpticStudio. He then sent the design file to the mechanical engineer, who loaded it into LensMechanix. They thereafter passed the design between OpticStudio and SOLIDWORKS without losing critical design data. “The communication piece with the mechanical engineer became much easier,” says Robert Mentzer, Optical Engineer. “It let me stay on an optics bench and in OpticStudio, and it let the mechanical engineer stay in SOLIDWORKS with LensMechanix and on his CNC machine,” he adds.
Global Surgical’s A-Series dental microscope
Based on the accurate design and accelerated schedule achieved on this microscope project, Global Surgical is standardizing on OpticStudio and LensMechanix to design future optical systems.
A Relentless Focus on the Power and Quality of the Software
Zemax’s mission is to facilitate companies that use optics in their products to develop the best-performing products more quickly at a lower cost and that remains the driving force behind the rock-solid physics architecture their software is built on. The company clearly cultivates a culture steeped in excellence and innovation and follows the approach of aligning with the customers’ feedbacks and requirements. The company aligns itself well with its customers’ success and that’s the reason they have been able to develop a vast client base across the globe.
Zemax’s software development is guided by their customer’s feedback and the trajectory of the industry as a whole and they back it up. From technical support to training and custom solutions, their engineering services team works towards eliminating all obstacles to customer success.“We have a grand vision of modernizing how teams design, build, and bring optical products to market faster. We’re perpetually iterating on our existing products, incrementally improving their capabilities, speed, and effectiveness,” adds Nicholson. “At the same time, we’re strategizing around breakthrough improvements, with new products in research and development and we are excited about what is yet to come.”
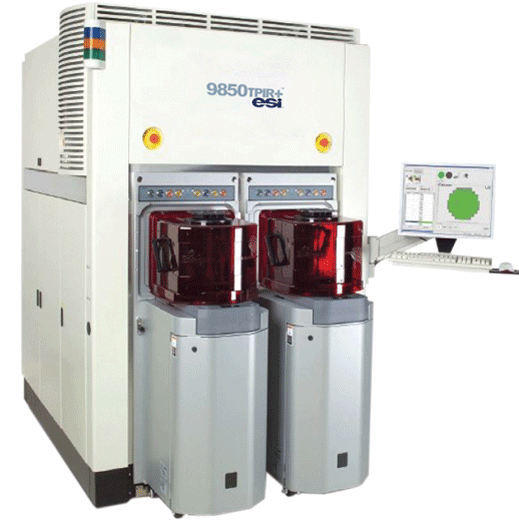
Incorporation of the OpticStudio and LensMechanix virtual prototyping environment helped in the successful mitigation of the challenge. OpticStudio and LensMechanix helped in the detection of optical model design errors months ahead of deployment. The optical engineer created the optical model for the eyepieces in OpticStudio. He then sent the design file to the mechanical engineer, who loaded it into LensMechanix. They thereafter passed the design between OpticStudio and SOLIDWORKS without losing critical design data. “The communication piece with the mechanical engineer became much easier,” says Robert Mentzer, Optical Engineer. “It let me stay on an optics bench and in OpticStudio, and it let the mechanical engineer stay in SOLIDWORKS with LensMechanix and on his CNC machine,” he adds.
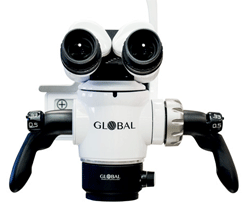
Based on the accurate design and accelerated schedule achieved on this microscope project, Global Surgical is standardizing on OpticStudio and LensMechanix to design future optical systems.
A Relentless Focus on the Power and Quality of the Software
Zemax’s mission is to facilitate companies that use optics in their products to develop the best-performing products more quickly at a lower cost and that remains the driving force behind the rock-solid physics architecture their software is built on. The company clearly cultivates a culture steeped in excellence and innovation and follows the approach of aligning with the customers’ feedbacks and requirements. The company aligns itself well with its customers’ success and that’s the reason they have been able to develop a vast client base across the globe.
Zemax’s software development is guided by their customer’s feedback and the trajectory of the industry as a whole and they back it up. From technical support to training and custom solutions, their engineering services team works towards eliminating all obstacles to customer success.“We have a grand vision of modernizing how teams design, build, and bring optical products to market faster. We’re perpetually iterating on our existing products, incrementally improving their capabilities, speed, and effectiveness,” adds Nicholson. “At the same time, we’re strategizing around breakthrough improvements, with new products in research and development and we are excited about what is yet to come.”
November 03, 2017

I agree We use cookies on this website to enhance your user experience. By clicking any link on this page you are giving your consent for us to set cookies. More info