THANK YOU FOR SUBSCRIBING
Digital Twin And Its Types
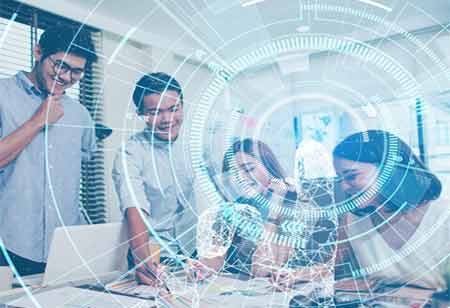
By
Apac CIOOutlook | Wednesday, April 20, 2022
Stay ahead of the industry with exclusive feature stories on the top companies, expert insights and the latest news delivered straight to your inbox. Subscribe today.
Digital twins were initially deployed in the cloud and typically created using IoT platforms. The platforms offered an IT architecture that included data management, analytics, and several services.
Fremont, CA: A digital twin is a dynamic virtual model that defines things created by synchronizing real-world data from numerous sources. As the target asset moves up from tiny (equipment) to large, the nature of the digital twin changes (a plant or city).
Digital twins were initially deployed in the cloud and typically created using IoT platforms. The platforms offered an IT architecture that included data management, analytics, and several services. As the usage of performance twins grew, constraints got discovered, and edge computing deployment options increased. In addition, 5G networks feature additional data communications capabilities for digital twins having widely scattered assets.
Different types of Digital Twin
Performance Digital Twin
Higher asset dependability and operational performance are aided by the performance digital twin in operations and maintenance. Analytics paired with both equipment and process data opens up new avenues for improving the dependability of industrial assets, allowing owner-operators to proceed toward near-zero unscheduled downtime.
Digital Twin Model
Algorithms mostly in twin model the asset and determine predicted values under normal conditions. When real-time data deviates from the expected value, the degradation gets identified. The degree of variation is helpful to forecast equipment breakdowns and the requirement for operator training.
Predictive Maintenance
Real-time data from operational equipment is collected. Process data is often obtained through the plant historian, while equipment data gets obtained via the Internet of Things (IoT). The model employs the first principles of arithmetic, machine learning, and artificial intelligence for analytics. PdM uses analytics to foresee failures and issue alarms by combining equipment and process data.
Maintenance happens when it is genuinely needed, i.e., immediately before process deterioration or equipment failure, with the efficiency digital twin deploying PdM. Improved uptime, asset longevity, maintenance costs, safety, schedule adherence, and income are advantages of proactive maintenance.