THANK YOU FOR SUBSCRIBING
Understanding the Digital Transformation Network
Organizations can reuse sub-solutions across various products to ensure consistent product quality.
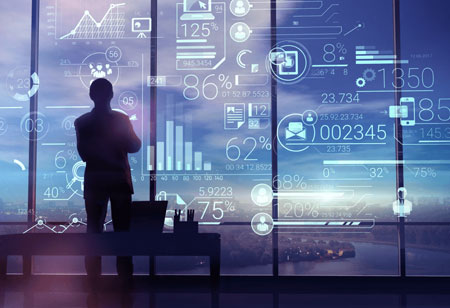
By
Apac CIOOutlook | Thursday, December 16, 2021
Stay ahead of the industry with exclusive feature stories on the top companies, expert insights and the latest news delivered straight to your inbox. Subscribe today.
Organizations can reuse sub-solutions across various products to ensure consistent product quality. These initiatives help companies achieve cost savings of up to 25 percent in growth, logistics, and production and a comparable reduction in time-to-market.
FREMONT, CA: Alongside solar power, the wind is the most mature form of driving and being driven by innovation. From a technological point of view, development in the wind industry can be seen through the cost of manufacturing equipment and delivery of energy and the growth of strategies such as modularization over the last decade. The ability to remotely control, locate, track, and repair equipment is an excellent example of the connection between technology and clean and efficient energy.
Transformation is a Network
Four main technological approaches epitomize the difficulty of disruption to bring about effective change. These include modularity, the use of digital twins, and digital Product Lifecycle Management (PLM), which then allows a single digital thread as the fourth tenet. The above addresses the need for a shared database where decisions can be taken more seamlessly, knowledge can flow more quickly, and practical and conjoined quality control systems can inform product innovations.
However, all four are interconnected with three key pillars in modularization, digitization, and hybridization, which help companies speed up growth and minimize costs by building on productivity levers. Modularization of product architectures gives consumers an improved preference. It allows economies of scale around the product life cycle using similar parts with various turbine designs, enabling existing machinery to adapt more quickly to new developments. The recurrent impact decreases unit costs and boosts efficiency.
Organizations can reuse sub-solutions across various products to ensure consistent product quality. These initiatives help companies achieve cost savings of up to 25 percent in growth, logistics, and production and a comparable reduction in time-to-market. Costs can be driven even further by digitization, where companies can discuss the linkage between all supply chain components to streamline operations and speed up the demand. Digital orchestration is the secret to facilitating this, as it provides a thread from design to production, or even design to serviceability, to streamline the operation and maximize performance and ensure improved consumer engagement at the moment.
The use of the correct purchasing model also lets companies conserve time and money. Changing from the Capital Expenditure (CapEx) model to the one driven by Operating Expenditure (OpEx)—or hybridization—will be crucial here. Rather than lavishly spending on sustaining physical components that will quickly be out of date, investing in resources that can be scaled up or down if required allows for more versatility.
Updating the industry’s commitment to innovation requires a dynamic network of quality development that is not mutually exclusive. Often the link between design, development, production, and after-market facilities is parallel, sometimes sequential. Irrespective of this, a systemic approach is required to take the sector forward entirely.
For example, improving artificial intelligence and analytics to build a digital twin for testing involves an appropriate PLM approach to ensure that the specification, design, and testing phases receive reliable and constant input and review. A single shared source of data and a digital thread are needed to inform consistency through this decision-making process, making projects such as the Digital Twin a much larger dialogue than just a discrete lifecycle level.