THANK YOU FOR SUBSCRIBING
IoT Significantly Improves The Preventive Maintenance Process
IoT enables the monitoring of the roller conditions in paper machines in the pulp and paper industries.
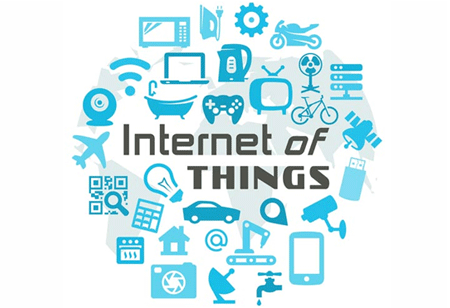
By
Apac CIOOutlook | Monday, May 13, 2019
Stay ahead of the industry with exclusive feature stories on the top companies, expert insights and the latest news delivered straight to your inbox. Subscribe today.
Prior to Industry 4.0, the preferred method for mitigating downtime and ensuring reasonably smooth equipment was the regular scheduled preventive maintenance. Since preventive maintenance is relied on regular cycles, it is inaccurate and expensive. It can be challenging to determine a correct maintenance schedule, sometimes resulting in an over-maintenance of machines that can raise the unnecessary downtime ironically. Increasingly, technology used IoT to execute efficient predictive maintenance procedures. A more holistic view of machine health can be provided by machine-included sensors–which are used to collect data sets and to send them via safe pathways to cloud-based platforms.
Incredibly, companies are turning to IoT-based monitoring of machine condition, which allows disclosing equipment problems that could impact product quality to be remedied before things get worse. IoT enables the monitoring of the roller conditions in paper machines in the pulp and paper industries. The standard of the paper produced can be greatly affected by a defect with a single roller bearing and fluffing and changes in paper thickness. To prevent a large percentage of quality problems, the condition of roller coils with vibration sensors is monitored. Vibration sensors constantly collect in real-time data on roller health at each end of the roller and transmit it to the cloud software. An IoT solution notifies an operator if the roller is not working properly.
The penetration of humidity into spaces and gaps in welded spots in the automotive industry can lead to porosity while temperature fluctuations in weld machines can lead to weld joint failure. To prevent incorrect placing and to guarantee high quality for the products welded, the IIoT applies to monitor the temperature and the moisture level around a machine.
Check Out : Top IoT Companies in APAC
As the IoT-driven condition monitoring solutions on the technology market are not yet available from the outside, companies need to develop and implement custom IoT applications. In cooperation with an IoT integrater, an IoT solution can be 'built' from the components that are tailored to the requirements of the company. Though IoT-based monitoring of conditions lays the groundwork for production quality enhancements, there are certain restrictions in this approach as data on the machine conditions are perhaps not sufficient for complete quality assurance. For example, monitoring the machinery condition cannot identify problems caused by the use of defective or misidentified components or inadequate handling of materials.
Since condition monitoring technology has become part of Industry 4.0, IoT significantly improves the preventive maintenance process. As IoT increases efficiency, manufacturers can expect lower costs, one of the main reasons why production experts are keen on IoT's role.